Classification characteristics
Ball valves are divided into: floating ball valve, fixed ball valve, orbital ball valve, V-shaped ball valve, three-way ball valve, stainless steel ball valve, cast steel ball valve, forged steel ball valve, ash discharge ball valve, anti-sulfur ball valve, pneumatic ball valve, electric ball valve, ferrule Ball valve, welded ball valve.
1. Floating ball valve
The ball of the ball valve is floating. Under the action of the medium pressure, the ball can produce a certain displacement and press tightly on the sealing surface of the outlet end to ensure the sealing of the outlet end. The floating ball valve has a simple structure and good sealing performance, but the load of the ball bearing the working medium is all transferred to the outlet sealing ring, so it is necessary to consider whether the sealing ring material can withstand the working load of the ball medium. This structure is widely used in medium and low pressure ball valves.
2. Fixed ball valve
The ball of the ball valve is fixed and does not move under pressure. The fixed ball valve has a floating valve seat. After being pressurized by the medium, the valve seat moves, so that the sealing ring is tightly pressed on the ball to ensure the sealing. Bearings are usually installed on the upper and lower shafts with the ball, and the operating torque is small, which is suitable for high-pressure and large-diameter valves. In order to reduce the operating torque of the ball valve and increase the reliability of the seal, oil-sealed ball valves have appeared in recent years. Special lubricating oil is injected between the sealing surfaces to form an oil film, which not only enhances the sealing performance, but also reduces the operating torque. , more suitable for high-pressure and large-diameter ball valves.
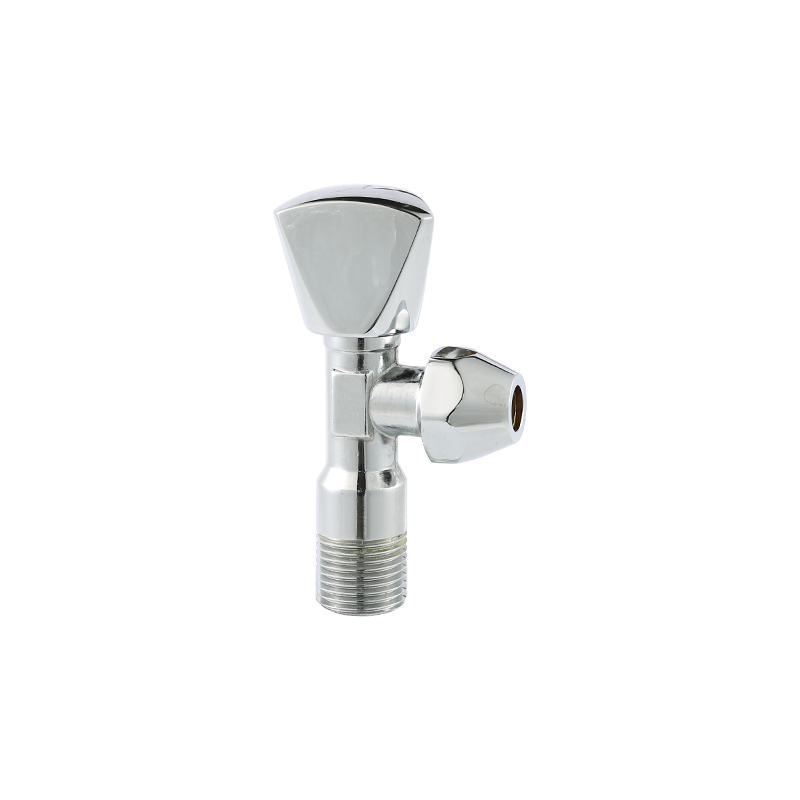
3. Elastic ball valve
The ball of the ball valve is elastic. The ball and valve seat sealing ring are made of metal materials, and the sealing specific pressure is very large. The pressure of the medium itself cannot meet the sealing requirements, and external force is applied. This valve is suitable for high temperature and high pressure medium. The elastic sphere is obtained by opening an Zinc handle, hand polish elastic groove at the lower end of the inner wall of the sphere to obtain elasticity. When closing the channel, use the wedge head of the valve stem to expand the ball and press the valve seat to achieve sealing. Before turning the ball, loosen the wedge head, and the ball will return to its original shape, so that there is a small gap between the ball and the valve seat, which can reduce the friction and operating torque of the sealing surface.
Installation Precautions
The disassembly and decomposition operation can only be carried out after confirming that the upstream and downstream pipelines of the ball valve have been depressurized.
Non-metallic parts should be removed from the cleaning agent immediately after cleaning, and should not be soaked for a long time.
During assembly, the bolts on the flange are tightened symmetrically, gradually and evenly.
The cleaning agent should be compatible with the rubber parts, plastic parts, metal parts and working medium (such as gas) in the ball valve. When the working medium is gas, gasoline can be used to clean metal parts. Clean non-metallic parts with pure water or alcohol.
Each disassembled ball valve part can be cleaned by dipping. The metal parts with undecomposed non-metal parts can be scrubbed with a clean and fine silk cloth impregnated with cleaning agent (to prevent the fibers from falling off and adhering to the parts). When cleaning, all grease, dirt, glue, dust, etc. adhering to the wall must be removed.
When the ball valve is disassembled and reassembled, care must be taken to prevent damage to the sealing surface of the parts, especially non-metallic parts, and special tools should be used when removing the O-ring.
After cleaning, it needs to be assembled after the cleaning agent on the wall to be washed has evaporated (it can be wiped with a silk cloth not soaked in the cleaning agent), but it should not be left for a long time, otherwise it will rust and be polluted by dust.
New parts also need to be cleaned before assembly.
Lubricate with grease. Grease should be compatible with ball valve metal materials, rubber parts, plastic parts and working medium. When the working medium is gas, for example, special 221 grease can be used. Apply a thin layer of grease on the surface of the seal installation groove, apply a thin layer of grease on the rubber seal, and apply a thin layer of grease on the sealing surface and friction surface of the valve stem.
During assembly, metal chips, fibers, grease (except those specified for use), dust and other impurities, foreign objects, etc., should not be allowed to contaminate, adhere or stay on the surface of the parts or enter the inner cavity.